How to Buy your First Laser Cutter
PURCHASING YOUR FIRST LASER CUTTER
Operating a laser cutter engraver at home involves 3 main steps, 1. General Considerations, 2. Workspace and 3. Maintenance. This guide will help you make the best decision when purchasing your new laser cutter.
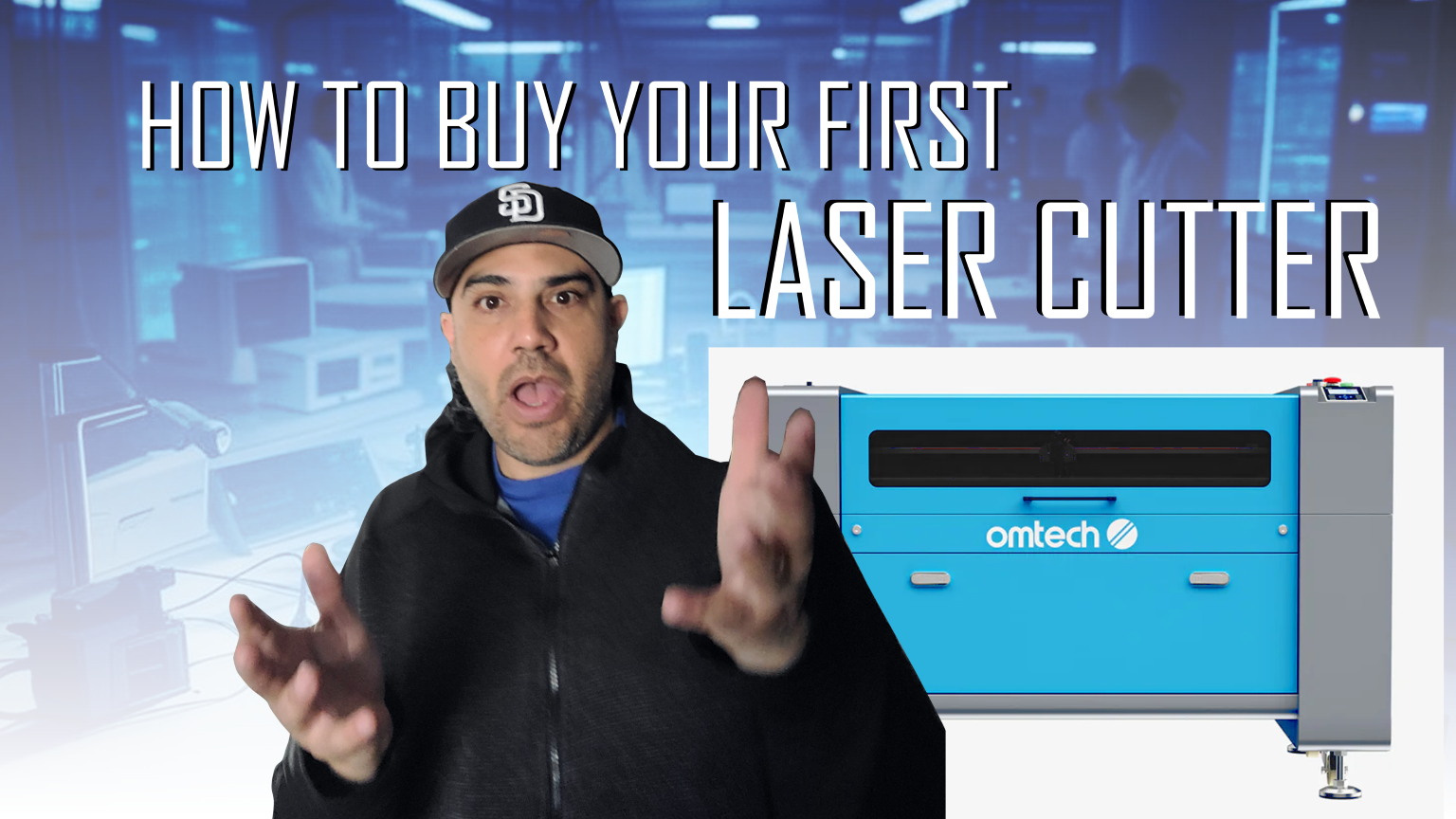
GENERAL CONSIDERATIONS
WHAT DO YOU WANT TO LASER CUT?
There are 3 types of lasers available for consumer and commercial use: CO2, Fiber and Diode Lasers, Each of these laser types is suited for different applications. Each type of laser operates at a different light wavelength which makes each type of laser interact with specific materials differently. There are also different power/wattage available for each type of laser which can greatly effect the speed and materials available for use. Here is a breakdown of the types of lasers.
CO2 LASERS: are the most versatile lasers because they can work with so many different materials. They use gas as a laser medium and are effective at cutting, marking and engraving wood, acrylic glass leather and lots of other materials. They require a water cooling system and ventilation/air assist to operate which makes for a bigger system for your home. CO2s also require the most maintenance of the three types but the pay off is the versatility of use.
Fiber LASERS: are your go to for laser cutting and engraving metals because they operate in a light wavelength that is absorbed by metals which gives you precise cuts. They are solid state lasers which means light is amplified through a doped optical fiber. Fiber lasers have better electrical efficiency and don't require water cooling for most applications. They are much less effective on materials like wood and acrylic but they have a longer lifespan overall.
DIODE LASERS: provide a better accessibility point for lasers in your home or small business and are the most budget friendly. They use semi-conductor devices to generate laser light which makes them great for engraving softer and thinner materials. Diode lasers are compact and generally don’t require a cooling system but the draw backs are that they operate slower and cant work with thicker materials. There has been some improvements in the diode technology so they have been putting out better options recently but beware of really cheap brands that don’t last.
So what are your Laser Cutter Goals? If your aim is versatility there is no question you need a CO2 laser which has limitations on metals but will work with almost anything else. If you wanna use metals in your materials Fiber is your only choice. Diode lasers are great to learn on but they are slow and only work well with thin materials. Getting a clear definition of your Laser Goals is crucial in making the decision on which laser cutter will meet your specific needs.
Here is a blog about setting up your laser: https://wellingtonjr.io/setting-up-laser-cutter/
BUDGET CONSIDERATIONS
I'm not going to go to much into budget because everybody knows their limitations in this area, but I will say that you will want to work with larger materials once you learn the basics on a laser.
SAFETY PRECAUTIONS
Always wear laser safety glasses specific to the wavelength of your laser. CO2 lasers typically require glasses that block 10,600 nm; fiber lasers might need glasses for 1064 nm; diodes can vary but often use 405-980 nm glasses.
All laser systems produce fumes and particles. Ensure you have adequate ventilation or an exhaust system to remove these byproducts. CO2 lasers especially produce a lot of smoke. Make sure you buy a smoke rated inline exhaust fan that will overcome the static pressure of your laser cutting system including any duct work which exits the building.
Keep a fire extinguisher rated for electrical fires nearby. Materials like wood or acrylic can catch fire when cut or engraved. Know your equipment, make sure you know about all the safety features of your specific laser model. Make sure your laser cutter is connected to ground per the manufacturers recommendation.
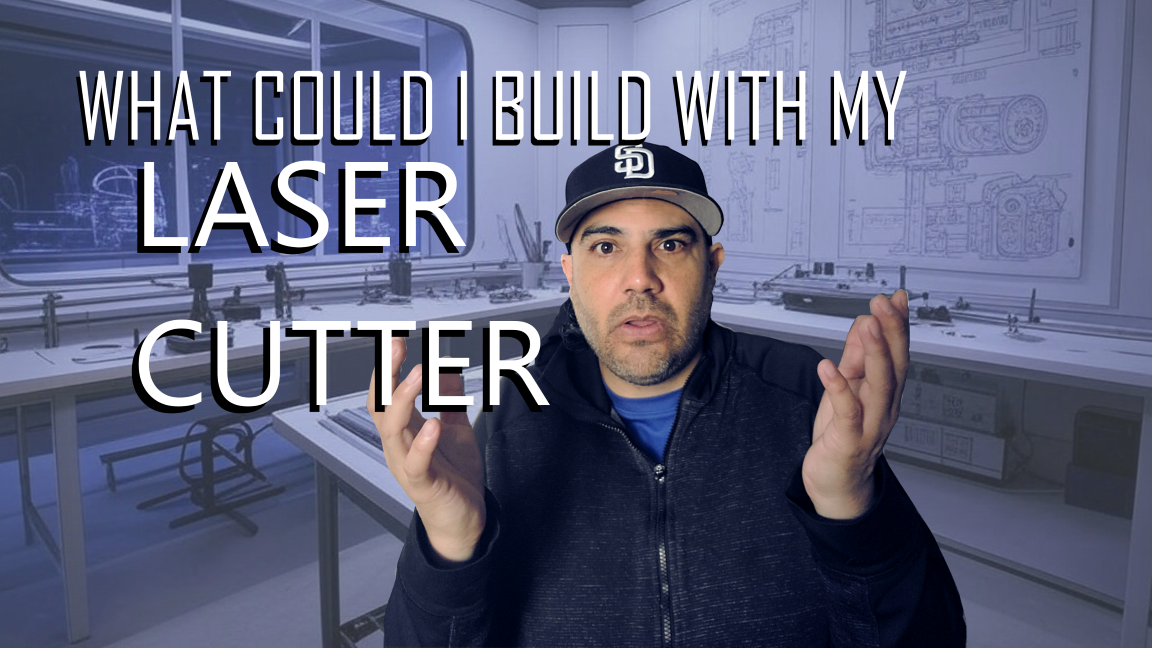
HOW I MAKE MY OWN PRODUCTS
Vector programs are a powerful tool for creating laser cutter files quickly. Before you select a laser make sure you are up to date on programs like Inkscape, illustrator or other vector programs. There are some free versions of vector programs so you could familiarize yourself with the vector format before you get a laser cutter.
Another hurdle is learning the laser control software for your specific laser. One of the industry standard laser control softwares is Lightburn which is the software I currently use. Laser control softwares allow you to import files, edit vector shapes and apply power and speed settings to your laser cut and engrave. I recommend doing a speed and power test when you get your laser or start working with a new material. The speed and power test will help you learn how the settings effect your materials.
CO2 Laser Workspace:
For a CO2 laser cutter, you'll need a substantial workspace due to the size of these machines and their associated equipment. A minimum of 10x10 feet is advisable, but more space might be needed depending on the machine's size. You should allow at least 3 feet of clearance around the machine for maintenance access, including the ability to open doors or panels for cleaning optics, replacing tubes, or aligning mirrors. The room should be equipped with an effective exhaust system or be connected to an external exhaust to handle the smoke and fumes produced during cutting, which can be significant with CO2 lasers. Consider also installing a chiller for cooling if your laser model requires one, adding to your space requirements. The floor should be stable and level to avoid vibrations that could misalign the beam or affect cutting precision. Lighting should be adequate but not directly above the machine to avoid reflections.
Fiber Laser Workspace:
Fiber lasers generally require less space compared to CO2 lasers due to their more compact design, but you still need room for operation and maintenance. A workspace of about 8x8 feet would be a starting point, ensuring at least 2 feet of clearance on all sides for maintenance tasks like changing lenses or focusing heads. Since fiber lasers often work with metals, consider the need for a safe area to handle hot or sharp materials. There's typically less smoke, but you'll still need some form of ventilation or dust collection, especially for fine metal particulates. The cutting bed might need regular cleaning or replacement, so having easy access for this is crucial. The machine should be placed away from direct sunlight or harsh lighting to prevent interference with the laser's operation, and the area should be kept free from reflective materials that could redirect the beam.
Diode Laser Workspace:
Diode lasers are the most compact of the three types, often fitting into smaller workshops. A workspace of 6x6 feet might suffice for smaller models, but you should still ensure 1-2 feet of clearance for maintenance, which mostly involves cleaning the laser head and checking or replacing diodes. These lasers produce less smoke than CO2 lasers but still require some form of ventilation, especially when working with materials like wood or acrylic. The setup for diode lasers can be simpler, often with less need for specialized cooling systems, but you'll want to manage heat, so good air circulation is beneficial. Since diode lasers can be less powerful, the workspace might also include areas for pre-processing materials or finishing work, depending on your project scope. Keep the area clean to prevent dust from accumulating on the laser head, which could affect performance.
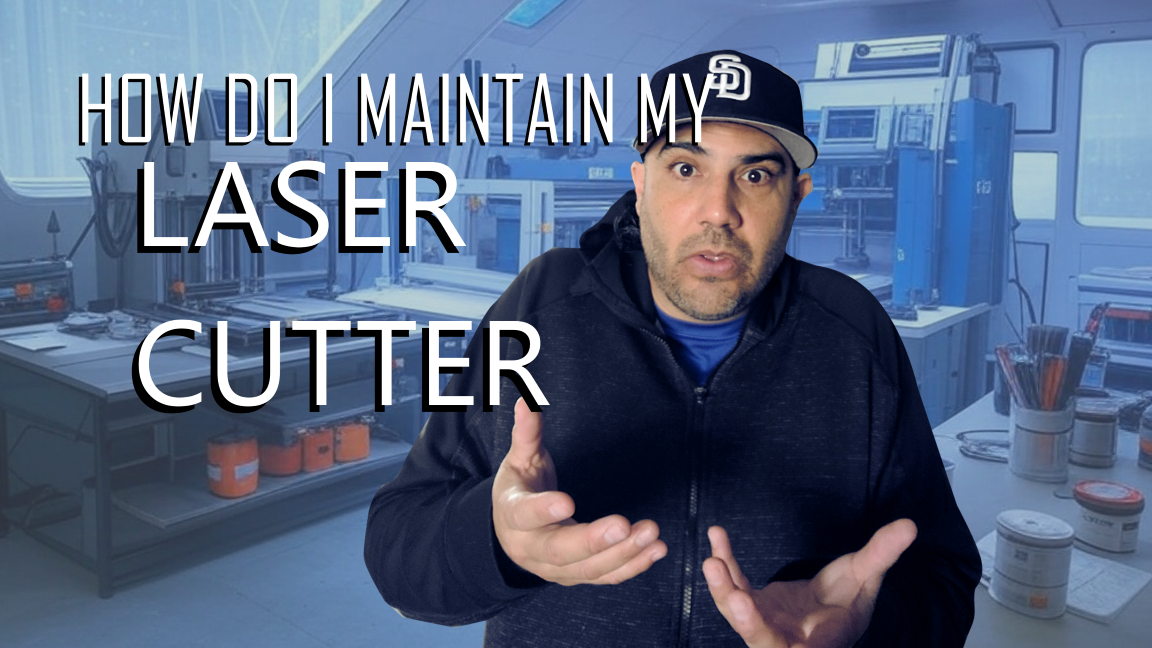
MAINTENANCE
Maintenance for CO2 lasers involves several key tasks to ensure optimal performance. Firstly, regular cleaning of optical components like lenses and mirrors is crucial since smoke and debris can cloud them, reducing beam quality and cutting efficiency. This should be done weekly or bi-weekly, depending on usage, using a mild cleaning solution and specialized lens tissue or cotton swabs. The laser tube, which can be filled with gas or water-cooled, might need periodic refilling or water treatment if it's a water-cooled system. Inspect and align mirrors as misalignment can severely impact the beam's path. The exhaust system needs regular checks to ensure it's effectively removing fumes; replace filters as needed. For machines with a water chiller, maintain the chiller by checking coolant levels and cleanliness. Also, look over the mechanical parts like the gantry and belts for any wear or looseness, lubricating or tightening as necessary.
Fiber Laser Maintenance:
Fiber lasers have fewer consumables and thus less frequent maintenance compared to CO2 lasers, but still require attention. The primary maintenance task is cleaning or replacing the protective lens or window at the cutting head, which can get dirty from metal particulates or other materials. This should be checked after every few hours of operation or when you notice a decrease in cut quality. The fiber optic cable itself should be inspected for any damage or kinks that might disrupt the beam. Check the cutting nozzle for wear or clogging, which can affect gas flow and cut quality. If your fiber laser has a chiller or cooling system, similar maintenance as with CO2 lasers applies here regarding coolant levels and cleanliness. Calibration of the laser power might be necessary if there's a noticeable drop in performance. Also, ensure that the machine's bed and surrounding areas are free from metal dust which could get sucked into the laser head or contaminate the workspace.
Diode Laser Maintenance:
Diode lasers require maintenance that's primarily focused on the laser diode itself due to their compact nature. Regularly inspect the diode for any signs of overheating or degradation, which might manifest as a decrease in power output or visible changes in the beam's quality. The laser head should be cleaned of any dust or debris that might accumulate, especially if you're engraving materials that produce a lot of dust. The cooling system, often air-cooled in smaller setups but sometimes water-cooled in more powerful systems, needs attention; ensure air vents are not blocked or clean the water cooling system if present. Check the focus lens for cleanliness as with other lasers, since any buildup can affect the beam's precision. For machines with moving parts, like those with a gantry system, lubricate and check for wear or misalignment. The diode might need replacement after several thousand hours of operation, so keep track of usage hours. Finally, ensure the power supply is functioning correctly, as diode lasers can be sensitive to power fluctuations.
SEND ME A MESSAGE FOR A FREE LASER CUTTER FILE
FOR A LEATHER WALLET